The fragility of global supply chains was glaringly apparent after the COVID-19 pandemic ground everything to a halt. Inadequate supply chain capacity planning caused sweeping shortages of essential goods for consumers and manufacturers alike—some of which may still stand today.
Just-in-time manufacturing may help facilities operate at maximum efficiency by eliminating high inventory costs. Yet the system builds in practically no fail-safe to rapidly respond to anomalies. Without predictive technology guiding production, or any stock to fall back on, there’s no room to adapt to unforeseen or rapidly changing circumstances.
The costs of this lapse are significant, both in terms of lost business and slowed growth. However, the inefficiencies and potential losses that manufacturers risk when their model includes extensive warehousing are a potential drag on healthy business margins. So, the ideal model should balance the efficiencies of just-in-time production with the stability of extensive inventory warehouses without the high costs.
Luckily, five emerging supply chain capacity planning solutions may help resolve this tension for manufacturers. Innovative technologies are driving some of these improvements, but others are simply the product of lessons learned during the supply chain breakdowns over recent years.
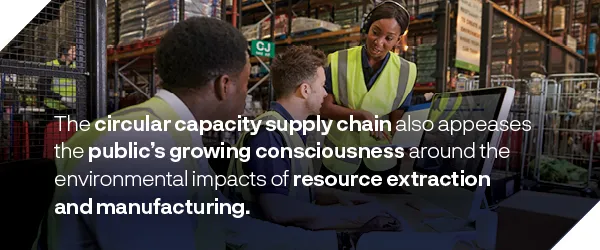
Using Circular Supply Chain to Minimize Environmental Impact and Maximize Value
The traditional progression of a supply chain is linear. Manufacturers source raw materials, refine them into products, and ship them to consumers. Then, eventually, consumers throw the products away. This straightforward manufacturing model has the clear benefit of not needing to plan for the afterlife of products. However, it may also produce significant material waste for landfills and oceans and assume an inexhaustible abundance of raw resources.
Of course, the growing concerns around environmental sustainability have been a wake-up call for manufacturers in terms of waste production. The finite nature of raw materials is becoming a more pressing problem.
The linear model might have worked in the past, but its inherently unsustainable nature is beginning to catch up with many industries. So, the alternative circular supply chain capacity planning strategy is quickly gaining momentum.
Manufacturers close the production loop by sending used products or parts back to be reused in production. This can help eliminate the harmful waste that clogs oceans and landfills as a result of manufacturing. It also simultaneously makes sourcing materials more affordable for manufacturers. Essentially, the circular capacity supply chain knocks out two birds with one stone.
At the same time, the circular model also appeases the public’s growing consciousness around the environmental impacts of resource extraction and manufacturing. Moreover, the circular model can help manufacturers align with the increasingly stringent emissions and waste generation regulations without cutting down production.
All in all, closed-loop production may offer significant benefits to manufacturers. But that’s not to say there are no downsides. Changing a linear manufacturing model into a closed loop requires upfront costs and significant logistical restructuring. Although, the long-term benefits of the effort have proved to be worth the initial challenge.
Using AI and Automation to Optimize Capacity Planning and Demand Forecasting
One of the biggest innovations that businesses across sectors are racing to incorporate into their daily operational planning is artificial intelligence (AI). The potential benefits of AI could fundamentally alter the functional capabilities of manufacturers in a variety of areas.
However, the strategic advantages it brings to supply chain capacity planning are perhaps the most notable emerging possibilities of the technology in the sector.
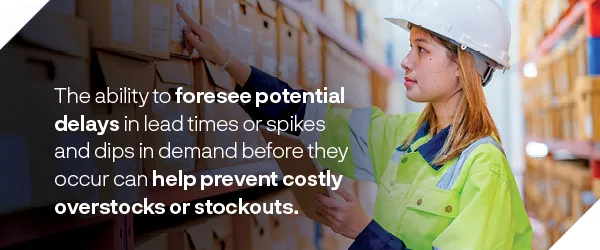
For instance, the drawbacks of just-in-time manufacturing are the unpredictability of spikes in demand or logistical breakdowns in the supporting supply chain. But what if these factors could be forecast ahead of time?
The ability to foresee potential delays in lead times or spikes and dips in demand before they occur can help prevent costly overstocks or stockouts. AI provides this capability by analyzing both historical and real-time data capture to spot hidden patterns that predict future market factors.
In response to these predictions, manufacturers may try to alter their workforce allocation, inventory levels, and production schedules. As a result, each facility scales its operational schedule up or down to meet exact market needs, improving profit margins.
By leveraging AI, manufacturers can also reduce the labor hours dedicated to manual data analysis. This helps ease the burdens associated with a tight labor market. It also frees up employees to work on higher-order tasks such as strategic planning.
At the same time, by analyzing vast amounts of internal and external data, AI can offer creative and cost-effective solutions like alternative materials or operational methods to improve production goals. In short, combining these benefits may give businesses an increased ability to adapt to changing needs and factors. But reliance on data can also present new challenges.
The Challenges of AI Supply Chain Capacity Planning
The business world has latched onto the revolutionary—and seemingly futuristic—benefits that AI and machine learning can bring. However, making such a fundamental alteration to operations in such a short time frame inevitably presents some risks.
First, AI may change how decisions are made. Potentially for the better, but only if the data it uses is reliable. AI relies on the information in data sets to provide the analytics that manufacturers will increasingly base their decisions on. So, if someone has corrupted the data or mismanaged it somehow, the resulting analytics will be faulty.
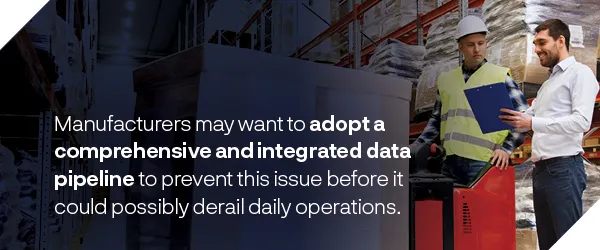
Manufacturers may want to adopt a comprehensive and integrated data pipeline to prevent this issue before it could possibly derail daily operations. But this often requires a costly upfront investment in IT technology. Plus, it takes time and resources to train and upskill the workforce on the new system’s workflows.
Data security has also become a notable challenge as business operations digitize. So, manufacturers should invest in robust digital security measures to prevent tampering.
Despite all these challenges, the costs of failing to adopt AI may outweigh its upfront investment fees in the long run. It can be difficult for manual data processing to compete with the added agility of AI integrations. Adopting AI may remain a strategic priority for many manufacturers across industries.
Using Elastic Logistics to Balance Supply and Demand Fluctuations
At this point, it’s clear that increasing operational flexibility and adaptability is most manufacturers’ response to unstable market conditions. After all, manufacturers can’t control materials shortages, economic instability, or unexpected climate shifts. But they can improve their responsiveness to these inevitable factors. Elastic logistics has quickly become a crucial way to improve supply chain capacity planning in the face of uncertainty.
AI integration is a key component of elastic logistics because it enables manufacturers to preemptively plan for future conditions. However, the concept of elastic logistics extends to a few other steps in the manufacturing process.
For instance, on top of AI-based production forecasting, companies can localize their supply chains through micro fulfillment centers. This makes it easy to ramp up shipping and deliveries in certain areas according to spikes in demand.
Similarly, manufacturers prioritizing elastic logistics often partner with third parties to improve their responsiveness. Logistics partners, in particular, may help manufacturers scale up the shipments and localized inventory for seasonal spikes in demand without investing wholesale in equipment and storage space.
Then, during periods of low demand, a manufacturing company may try to eliminate these costs to rebalance its budget quickly. As a result, logistically elastic companies optimize their portfolio at all times.
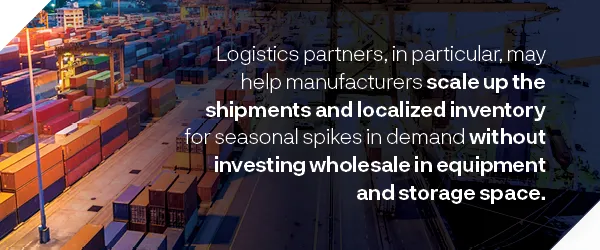
Using Scenario Supply Chain Capacity Planning to Assess and Address the Market
Scenario planning is the process of sketching out responses to different market conditions. These potential scenarios can be real, but the issues that scenario planning takes care of are often hypothetical.
For example, factors such as an economic recession, emerging social trends, or potential regulation changes can all be played out to develop the best tactics to handle them. Alternatively, the scenarios can be positive challenges, such as an unexpected spike in demand that leaves a manufacturer without enough capacity.
Essentially, this may help a manufacturer create a well-thought-out plan for navigating potential issues to create immediate action should that problem occur. The key advantage garnered through this strategy is response time.
By following a predetermined blueprint for responding to the issue, companies can be sure that their response isn’t impulsive while also enacting it quickly. Scenario planning also allows leadership teams to engage in non-linear creative thinking that could help them come up with innovative solutions to existing issues.
Of course, the apparent downside of scenario planning is the time and resources required to conduct the process. Dealing with problems that haven’t actually occurred can seem exorbitant to operations with slim margins. Yet proponents of the practice often consider this thinking to be short-sighted.
Over time, it’s likely and even inevitable that some or all of the planned scenarios will occur. Considering this, the potential savings that result from a pre-planned response are hard to count but could be significant.
In a volatile market, such as manufacturing in the post-Covid lockdown era, risk management investments pay notable returns. So, while the costs of scenario planning may be high, the returns will most likely be worth it.
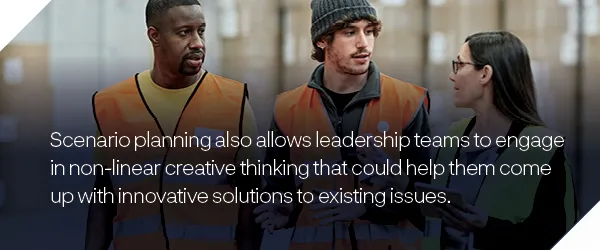
Using Collaboration Platforms to Improve Visibility and Coordination Across the Supply Chain
At the end of the day, strong lines of communication are what hold the global supply chain network together. Managing logistics across oceans, mountains, and leagues is no small feat. It requires a cohesive system of interconnected moving parts to all work together.
Of course, this means that little breakdowns in one part of a system can create waves all around the world. Therefore, especially in volatile times, communication channels are of paramount importance.
The tools available to facilitate intercontinental communication have never been more sophisticated. Collaboration platforms, in particular, instantly transmit granular details and real-time updates to supply chain partners. These platforms serve as centralized hubs where manufacturers, suppliers, distributors, and retailers can access and update information in real time, from inventory levels to shipment tracking.
At the same time, the best versions of collaboration software harness the latest data privacy tools to create a secure environment. This way, shared portals can safely transmit sensitive information. This can help keep entire supply chains in line with guidelines and regulations regarding digital security.
The benefits of collaboration platforms are numerous. To start, the efficiency of communication between companies is unparalleled. There’s no need for extensive back-and-forth emails or phone calls. Instead, all the information is shared collectively through a central channel. As a result, it’s easier to access and see both updates and general information.
Simultaneously, this improved flow of information fosters greater trust between partners through transparency. All parties may monitor progress and more easily anticipate potential challenges.
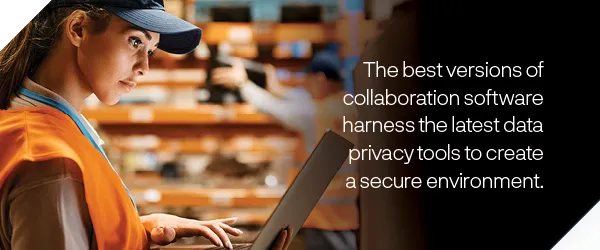
Leveraging a Financial Partner for Supply Chain Capacity Planning
Most would agree that the pandemic left many global supply chains in shambles. But in rebuilding these disrupted communication and shipping lines, the industry has the opportunity to modernize, strategize, and improve its daily operations.
Objectives like improving communication, initiating scenario planning, implementing elastic logistics, integrating AI, and moving toward a circular supply chain model are all key steps along the way. However, the major obstacle to overcome here is the upfront investment cost necessary to make these improvements. In this regard, each manufacturer needs a customized assessment of their individual financial factors to determine which objectives are cost-effective for them.
The partners at Arizona Bank & Trust, a division of HTLF Bank can help manufacturers navigate the financial side of supply chain operations. They can leverage their experience and knowledge regarding investing, savings, and corporate budgeting to improve your supply chain capacity planning initiatives.
Extensive financial analysis is critical when it comes to smart investing. The customized advice of a financial partner can help slim down the cost of change. Reach out to speak to a commercial banker at Arizona Bank & Trust, a division of HTLF Bank today.
These links are being provided as a convenience and for informational purposes only; they do not constitute an endorsement or an approval by HTLF of any of the products, services, or opinions of the corporation or organization or individual. HTLF bears no responsibility for the accuracy, legality or content of the external site or for that of the subsequent links. Contact the external site with questions regarding its content and privacy policy.